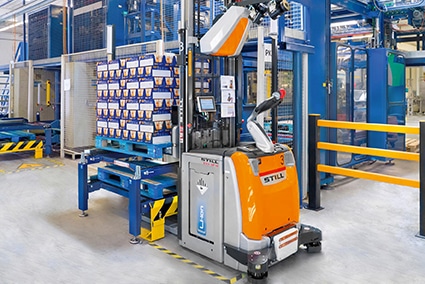
Nestlé a choisi les solutions de Still pour mettre en place, dans son usine de Biessenhofen, un système de transport intelligent en alimentant les lignes de production du site en flux continu, 24 h/24 et 7 j/7. Par Catherine Batteux
Avec des allées de circulation très exiguës, l’usine de Nestlé de Biessenhofen, en Allemagne, devait gérer de nombreux goulets d’étranglements et des encombrements chroniques en entrée et sortie des machines de production. L’entreprise s’est appuyée sur Still pour réorganiser son intralogistique en intégrant l’automatisation avec, pour challenge, de ne pas interrompre la production. Quatre gerbeurs automatisés EXV iGo et un Pallet Shuttle ont été déployés et permettent une augmentation des flux, davantage de flexibilité et une meilleure sécurité des processus.
Lisser les flux
Les gerbeurs automatisés remplissent chez Nestlé de multiples fonctions : ils transportent les matières premières et les emballages jusqu’à la production ; ils prennent en charge l’enlèvement des matières recyclables et le restockage des palettes vides. Grâce aux AGV (Automated Guided Vehicle), les lignes de production sont approvisionnées de manière flexible et continue 24 h/24 et 7 j/7. Le mode de production a pu ainsi passer de la méthode « flux poussés » à la méthode « flux tirés », donc beaucoup plus en flux tendus. Chaque ligne de production ne draine désormais que des palettes individuelles avec des matières premières et des emballages. Cela a permis de libérer les surfaces auparavant occupées par les stocks de pré-production encombrant les lignes, tout en lissant les flux d’approvisionnement.
« Le transport s’organise tout seul »
Equipés d’un scanner laser à 360°, les AGV circulent en toute sécurité dans les allées exiguës et sinueuses. « AGV, piétons et chariots élévateurs peuvent circuler conjointement sur le parcours sans incident, ce que n’aurait pas permis un système de convoyeurs fixes qui n’aurait fait qu’obstruer inutilement en permanence les allées de circulation », raconte Bruno Chambraud, responsable du département Intralogistique chez Still France. Dès que la production signale un besoin au sein de SAP, un ordre de transport est déclenché dans le système de convoyeurs faisant l’interface avec l’entrepôt. Les capteurs inductifs des convoyeurs déclenchent les missions des AGV. Avec la priorisation des ordres, chaque AGV reconnaît quel convoyeur doit être desservi en premier. « Il n’y a pas d’interface informatique entre la boucle de commande Still et le système hôte Nestlé. Le transport s’organise tout seul », ajoute-t-il.
Flexibilité
La nouvelle organisation logistique avait également pour projet de supprimer 6 entrepôts stockant des emballages et des accessoires de production afin de les regrouper en une seule infrastructure. Un entrepôt avec un système de rayonnage par accumulation desservi par la technologie Still Pallet Shuttle a été mis en place pour les emballages industriels et les europalettes. Ainsi, les navettes et le chariot desservant les couloirs du nouvel entrepôt travaillent simultanément. Avec le stockage et la récupération semi-automatisés, chaque couloir d’accumulation gère indépendamment son remplissage de marchandises. De quoi apporter davantage de sécurité, de rendement, de densité et de souplesse. Les pics de commande peuvent ainsi être traités rapidement et avec une grande flexibilité grâce à la mobilisation simultanée de tous les couloirs et de toutes les navettes.